Soaring five times the speed of sound or more in the near future, our nation’s military and aerospace industries are looking to bring hypersonic-capable vehicles into their fold. However, the research road to Mach 5 and beyond is long and arduous.
“This is not an incremental difference. It’s a massive gap,” says Andrey Voevodin, associate dean for research and materials science and engineering professor in the College of Engineering at the University of North Texas. “You cannot use the same materials, the same alloys or even the same instrumentation.”
UNT can help lessen that gap thanks to its team of engineering experts and top-rate facilities across the university. The Materials Research Facility (MRF) at UNT’s Discovery Park is a unique center for multi-scale and multi-dimensional characterization of materials, including those relevant for hypersonics.
“This is not an incremental difference. It’s a massive gap. You cannot use the same materials, the same alloys or even the same instrumentation.”
-Andrey Voevodin, associate dean for research, UNT College of Engineering
Additionally, a novel X-ray diffraction system, specifically designed for analyzing hypersonics-related materials, is being developed and installed at UNT. Meanwhile, the Center for Agile and Adaptive Additive Manufacturing (CAAAM) is bringing material synthesis and manufacturing into the future through its state-of-the-art infrastructure and faculty specializing in the comprehensive additive manufacturing science of advanced materials and 3D printing.
Hypersonic Challenge
Today, aerospace vehicles are constructed using materials made from a mixture of metals called superalloys capable of withstanding high temperatures. Current jet engines can reach about 2,000 degrees Celsius inside the combustion section. Most of the superalloys fail at around 1,300 degrees Celsius. To protect them, the aerospace industry uses a protective ceramic coating or thermal barrier coating manufactured over the superalloy.
However, for hypersonic speeds, the alloys and ceramics need to withstand temperatures approaching 4,000 degrees Celsius. That’s nearing surface of the sun temperatures, which is usually about 5,500 degrees Celsius. “All of these current materials and ceramics fail rapidly at such extreme temperatures,” Voevodin says.
Finding materials that fit the temperature requirement isn’t the only challenge researchers face. The act of studying and testing these materials also is challenging. A person cannot stand next to a material at that temperature without protective gear from the heat radiation. Most tests are performed with researchers in a separate room. For the test, a gas torch is hooked up to an oxygen or other combustion gas feed and then fired at the material. Researchers watch the process through a glass window or infrared camera. “But you’re not measuring anything. You can only see if it breaks,” Voevodin says.
The flames from the torch are so hot, any measuring equipment would melt or break during testing. Researchers cannot test if a ceramic can bend at 4,000 degrees Celsius or how the microstructure of an alloy changes as it is heated. Voevodin says there is no lab in the U.S. capable of such measurements under extreme conditions, not even within the U.S. military. But UNT researchers will soon change that.
Closing the Gap
Voevodin and his UNT colleagues — Samir Aouadi and Marcus Young — are collaborating with the U.S. Army Research Lab on a few projects to bring hypersonic research capabilities to the U.S.
The first is a $2.6 million grant to develop a one-of-a-kind X-ray diffraction system at UNT’s Discovery Park capable of reaching the extreme temperatures needed for hypersonic speeds while allowing property measurements of protective materials upon heating under extreme conditions.
The system’s design is being led by Young, a materials science and engineering associate professor. Once in operation, the system will be open for use by UNT and U.S. Department of Defense scientists.
“Right now, it’s not possible to observe high temperature behaviors,” Young says. “This system is going to allow us to answer those questions of can we control alloy shape morphing, can we control the ceramic that covers it, can we create a stable structure that will last longer at these extreme temperatures?”
Young is working with analytical instrument manufacturer Rigaku to design the machine, which they expect to be operational by Spring 2025. Instead of a gas torch, it will use a laser beam to heat the materials. The laser will apply a more centralized ultrahigh temperature onto the surface of the material.
“We’ve been in talks with multiple companies over years about this system,” Young says. “You tell them you want to put a laser into the system, and they say it’s too complicated. It is complicated, but we need to do this. Rigaku has been a great collaborator for us in working to make this system a reality.”
New Materials
UNT researchers also are creating materials capable of withstanding hypersonic conditions. While all of them have a background in aerospace and high temperature research, each team member plays a specific role in moving the research forward.
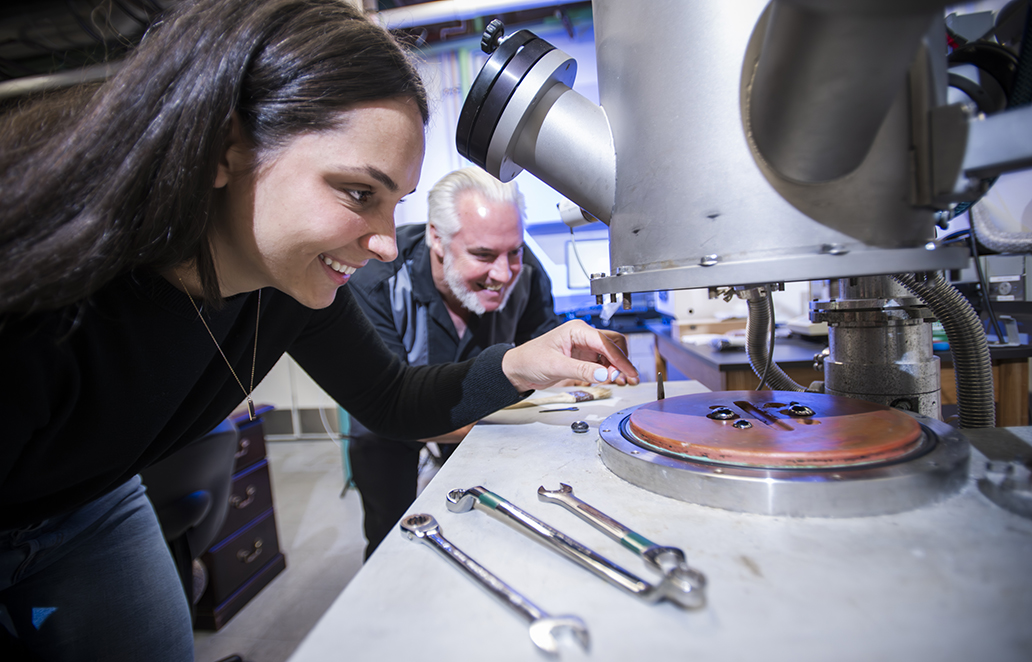
Young, who specializes in alloys and ceramics, focuses on developing ultrahigh temperature shape memory and shape morphing alloys. The alloys are capable of changing to a predetermined shape they “remember” when exposed to a high temperature, an electrical current or responding superelastically to a bending force, such as those experienced during hypersonic flight.
Aouadi focuses on the ceramics side of the project. The selected ceramics would consist of coatings that are produced over the alloys to help protect them from the heat generated by hypersonic speeds.
“We are taking a very different approach by using a mix of high temperature ceramics,” Aouadi says. “There are very few compounds that won’t melt at 3,500 degrees Celsius. Since we know what those are, now we just have to focus on selecting the right ones that facilitate the shape morphing aspect, which we’ll be able to study with the new system.”
Aouadi is producing high temperature ceramic matrix composites for testing. Ceramic fibers are weaved together on a microstructural level to make the final component less likely to crack. Common fibers used for these composites are carbon, silicon carbide and alumina. Similar to pottery, the idea is for the final ceramic material to be durable at room temperature, but as it heats up, it should become malleable and bend with the shape morphing alloys.
Meanwhile, Voevodin is an expert in heat dissipation across a material and controlling heat during testing. With the three working together, they account for each main part of the hypersonic equation — the alloys, the ceramics and the temperature. “We are creating the foundation here at UNT,” Voevodin says. “We are preparing our students to work in this hypersonics realm and carry the torch to develop vehicles society could use for aerospace transportation in the decades to come.”
One such student is doctoral candidate Sophia Cooper, who has been with the team since 2020. “It’s been challenging, but rewarding,” Cooper says. “Sometimes it’s difficult to gauge the progress you’re making, but our meetings with the army researchers show that the work we are doing at UNT is meaningful.”
Cooper is developing high temperature shape memory alloys that can withstand hypersonic speeds for up to one hour. Her alloys are based on a mixture of nickel, titanium and zirconium. She’s also added in copper and niobium to tailor material properties. “I have come to find that research is a lot of failure before progress.”
Initial studies demonstrated that shape memory alloys made with zirconium were difficult to process or shape, according to Cooper. Most existing research instead uses a mixture with hafnium. Other research even uses gold, palladium and platinum. Cooper says zirconium has been hard to work with but she intends to stick with it.
“Zirconium is a lot cheaper than hafnium and the other materials. It’s also more lightweight. My hope is we can find a solution that will create a more commercially viable alloy for these applications.”
Cooper uses equipment in Young’s X Lab: Metallic Processing and Characterization for her work, such as an arc melter that melts the metals together and a rolling mill that converts the metal to a plate or rod. She then rolls the alloy and repeats the rolling process until it reaches the desired thickness. “There’s a lot of problem solving that goes into it. It’s been the most fun and the most challenging.”
Her alloys, which will be shielded by the ceramics, operate at a much lower temperature of up to 500 degrees Celsius. Since the operating temperature is lower, it allows her to study the alloys more closely to find a viable path forward for zirconium. She’s able to use more equipment to study the alloys as they transform upon heating and cooling. One technique she uses is differential scanning calorimetry, which allows her to see the specific temperatures where these phase transformations happen.
At the Army Research Lab’s Aberdeen Proving Ground in Maryland, she and army researchers there have used transmission electron microscopy to give insight into the materials’ behaviors at an atomic scale.
“Oftentimes, you feel like you’re moving backward, but that’s not the reality. Otherwise, great discoveries would never have been made,” Cooper says.
Changing Manufacturing
Across the hall from the Materials Research Facility is the Center for Agile and Adaptive Additive Manufacturing (CAAAM), which has secured $30 million in funding from the Texas Legislature since 2021 for its innovative research. As faculty like Voevodin, Aouadi and Young find the mixtures needed to make materials capable of hypersonic speed, CAAAM researchers focus on how to create the final components.
“They know the properties they need, but fabricating the components by conventional technology and manufacturing processes is very difficult,” says Regents Professor Narendra Dahotre, who serves as CAAAM associate vice president and founder. “That’s where additive manufacturing and 3D printing come into the picture.”
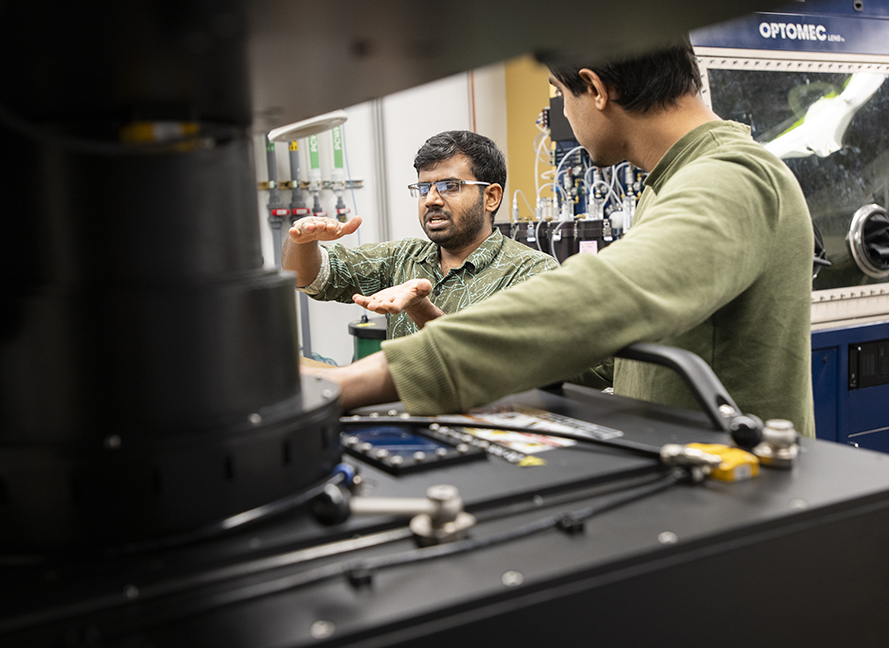
UNT faculty affiliated with CAAAM have expertise in advanced materials, such as Voevodin, Aouadi and Young, and in additive manufacturing like Dahotre. It’s also home to state-of-the-art and specially made customized machinery for additive manufacturing research of high temperature refractory materials. There are two types of machines used for their research — a laser powder bed machine and laser direct energy deposition machine.
For the laser powder bed machine, a laser moves over a bed of powder material, typically a pre-alloyed powder or elemental powder blend, and fuses the mixture layer by layer into a component shape like a gear.
“It’s like watching something rise out of a tank of water, but it comes out of loose powder,” Dahotre says.
The laser and a powder dispenser move together in the laser direct energy deposition machine. The powder is injected into the beam and the molten drops fall onto a substrate layer by layer to form the component.
“A hypersonic jet engine for an airplane and a hypersonic jet engine for a space shuttle are both engines,” Dahotre says. “But their requirements are different from one another which means the components’ properties will be different. Our research is studying the fundamental science of these manufacturing processes.”
Regents Professor Rajarshi Banerjee in materials science and engineering is another member of CAAAM and MRF director. Like Dahotre, he studies alloys currently used in aircraft and their viability if made through additive manufacturing.
“We compare these microstructures and compositions to conventionally made alloys,” Banerjee says. “If they’re similar, then we’ll have an idea that the additively manufactured component will survive the same conditions before we move to simulated testing.”
The work, funded by the U.S. Air Force Office of Scientific Research and guided by the Air Force Research Lab, is carrying out fundamental science on developing next generation high temperature alloys for hypersonics, including refractory high entropy alloys and their processing using additive manufacturing or 3D printing. “Our research on 3D-printed alloys has potential to impact mass production of components for aircraft in the future.”
CAAAM researchers also test the components they create with these alloys to see if they are capable of withstanding high temperatures. However, they run into the same problem as before: they can’t test the component as it’s being heated. “We would love to be able to test these components in a dynamic environment, but there’s no equipment that can sustain an environment approaching 4,000 degrees Celsius that lets you see what’s happening on a microscale at the same time,” Banerjee says.
“We are ahead of most labs in the country with our center. Not many labs in the world have the kind of infrastructure CAAAM has for 3D printing. Many researchers understand the issues at play for hypersonic capabilities, but they can’t work on it because they don’t have the unique capabilities we have.”
-Narendra Dahotre, CAAAM vice president and founder
That’s where the future X-ray diffraction system will come into play. For now, teams at CAAAM perform lower temperature post-processing testing on components looking at properties such as mechanical, grip and fatigue strength. After that, they use computation models to project how the components will behave at higher temperatures.
Conventional manufacturing and the current commercially available version of additive manufacturing cannot produce multimaterial and multilevel microstructures on-site and on-demand like CAAAM’s machinery can.
“We are ahead of most labs in the country with our center. Not many labs in the world have the kind of infrastructure CAAAM has for 3D printing,” Dahotre says. “Many researchers understand the issues at play for hypersonic capabilities, but they can’t work on it because they don’t have the unique capabilities we have.”
Full Speed Ahead
Teams at the MRF and CAAAM mainly work with the U.S. Department of Defense to explore ways to make hypersonic vehicles for the U.S. military. However, there are other applications for hypersonic capable components, such as fusion energy and future transportation.
“The inside of a nuclear reactor has an extremely high temperature and high pressure so there could be a cross compatibility that CAAAM is exploring,” Dahotre says.
The future also could bring hypersonic travel on Earth and in space. A hypersonic transatlantic flight from Dallas to London, for instance, would only take one hour. “We could even reduce the size of everything,” Dahotre says. “If you look at the model of a space shuttle, the part the human sits in is very small, everything else is related to the engine.”
Hypersonic vehicles could help the environment, too. Both Voevodin and Dahotre say the hotter an engine burns, the more efficient its fuel usage is, meaning hypersonic vehicles would use less fuel and produce lower carbon dioxide emissions.
“If you look back in history, the military is always on the front line,” Voevodin says. “A decade later commercialization starts. I think the same thing is going to happen here and that’s why I’m excited to work on this. This will be a game changer, and it’s starting here at UNT.”