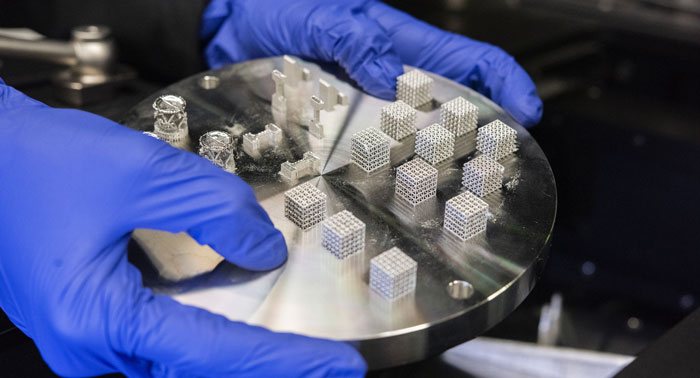
It is a time of marvels and miracles, a time when 3D objects can literally be printed from a computer. Look around. It’s the Fourth Industrial Revolution, where manufacturing design, process and production are combining into one comprehensive whole. New technology is leading industry into the age of additive manufacturing where it will be possible to design and print a final product using only the materials needed without ever leaving your chair.
“The uses for additive manufacturing have the potential to transform a wide variety of industries — from the oil fields to the operating rooms,” says Narendra Dahotre, interim vice president for research and innovation at UNT. “Imagine knowing exactly what you want to create, exactly how much it will cost, exactly how much materials will be needed and exactly how long it will take to complete. Additive manufacturing is the industry’s dream come true.”
At UNT, researchers are probing the possibilities of additive manufacturing through its highly advanced Additive Manufacturing Laboratory. The lab is located within UNT’s College of Engineering right next to the Materials Research Facility in Discovery Park, the North Texas region’s largest research park. UNT is the only university in the nation with this configuration across fields to better advance the science and application of additive manufacturing. The lab is one of the key assets being leveraged in UNT’s new Center for Agile and Adaptive Additive Manufacturing (CAAAM) to move Texas further along in advancing additive manufacturing technologies and meeting the growing demands for additive manufacturing of high-performance and functionally efficient advanced materials.
Perfecting the process
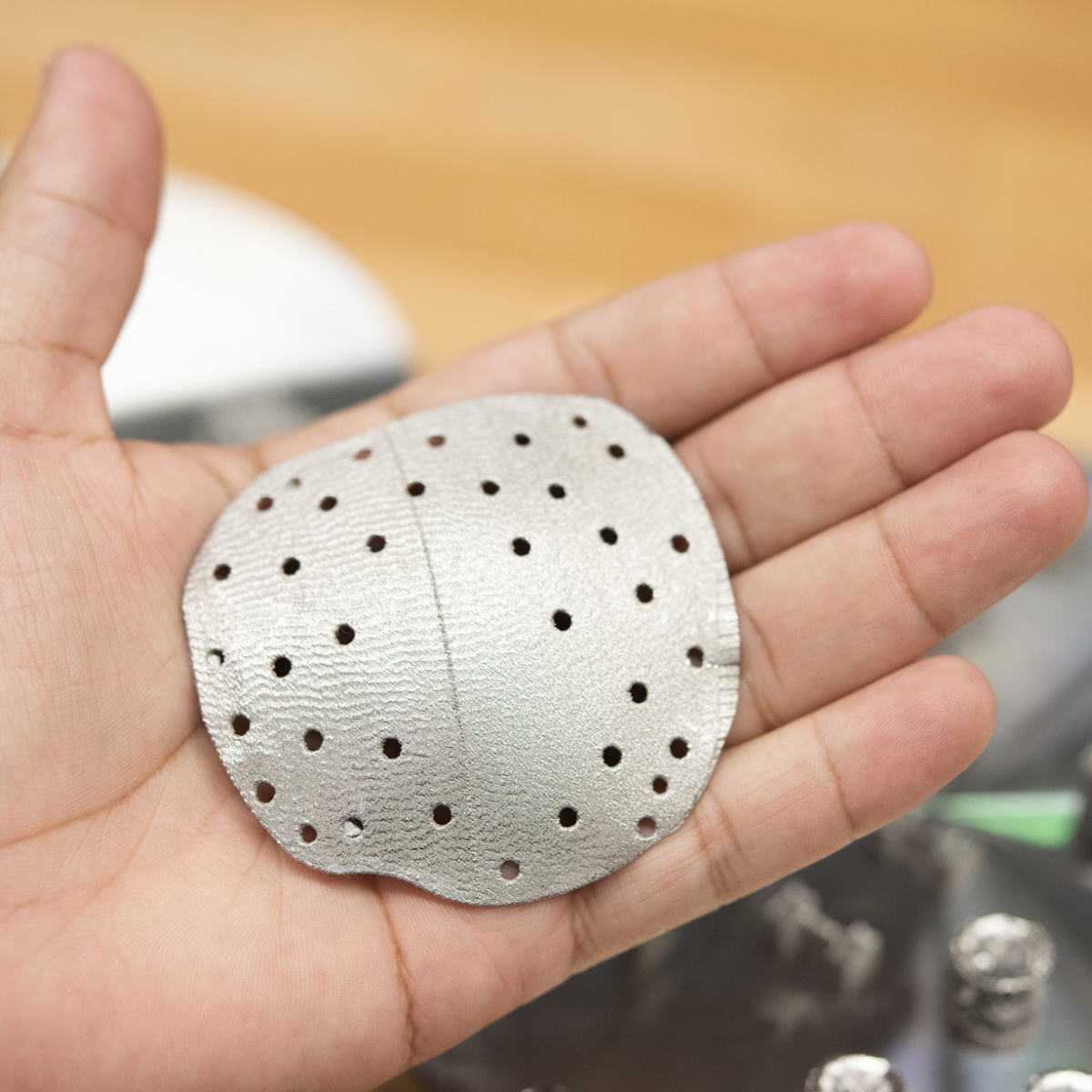
Additive manufacturing may sound complicated, but the theory isn’t. Instead of building a sandcastle by subtracting sand away from a pile until the structure appears, imagine adding sand beginning at the bottom and moving up layer by layer until a castle is built. In the actual application of additive manufacturing, the grains of sand would be placed one at a time in a specific order pre-determined by an enhanced computer design.
“Additive manufacturing is a new area of engineering,” says Rajarshi Banerjee, Regents Professor and director of UNT’s Materials Research Facility. “As such, there are many unexplored areas and unanswered questions. For example, we are finding that the structure of certain metallic materials has fundamentally changed after going through this process. The aluminum alloy powder used to create a component using additive manufacturing technology may look the same and be chemically similar to those produced using traditional manufacturing, but it has a different microscopic structure and properties. The question we are trying to answer is ‘Why?’”
At this time, most additive manufacturing involves plastics and polymers. UNT has taken the materials involved several steps further to include metals, ceramics and metal-ceramic composites. Due to the change that occurs to materials during processing, Banerjee’s research also involves the creation of additive manufacturing-specific alloys. These alloys are better adapted to additive manufacturing processes and provide for a consistent end product.
Additive manufacturing is capable of producing higher-strength and more energy-efficient materials while reducing the actual amount of materials needed, wear and tear on parts and use of natural resources. The shapes created are anything but simple. These shapes can be hollow and contain other hollow, internal shapes like Russian nesting dolls. This allows for the printing of objects from struts to gears to be printed inside the primary shape as it is being created.
“For UNT, it’s not just about the research,” Banerjee says. “The lab will provide a platform for education where students and faculty will be exposed to the latest technology and in turn provide a trained workforce for the future of manufacturing.”
Transforming industry
There was a time when designers, architects and engineers would sit for hours at a drafting table creating blueprints for everything from small toys to automobiles. Then, with the advent of computers, computer-aided design and drafting (CADD) became an everyday tool. Users could produce 2D drawings, correct and modify them, print them out on paper as a final draft and then build a 3D model.
Now, UNT students and faculty have moved beyond the drafting table, beyond 2D CADD and beyond hand-made models. Utilizing the latest in CADD programming and 3D printing, additive manufacturing users at UNT will develop the skills needed to design and manufacture products in an ever-changing industry. But this doesn’t just apply to students and researchers using the Additive Manufacturing Laboratory. UNT libraries operates The Factory, an innovation lab/makerspace with two locations on campus. These spaces are used to provide students from all disciplines with access to equipment, software and training — including 3D printers and CADD systems — to promote innovative, cross-disciplinary learning.
In a 2016 Nature Materials article, “Policy Needed for Additive Manufacturing,” the authors point toward a future where additive manufacturing must go hand-in-hand with materials science — which is exactly what happens at UNT. The article also goes on to state that the best way for industry and future workers to learn is to “learn by doing.”
“By providing students and researchers with all of the current tools needed in not just additive manufacturing but materials science and general engineering, UNT is creating the next generation of investigators and technicians who will not only work in the additive manufacturing world but also help bring about the next stage in advanced production,” Banerjee says.